All Articles
Trending Articles
What Is a POS System and How Does it Work? Everything You Need to Know
A point of sale (POS) system used to be a cash register that simply recorded the day’s sales and organized your cash into sections. With today’s technology, however, a POS ...
Best Point Of Sale Systems
What Is a Sales Growth Calculator? How It Works and Why It Matters
What is Sales Growth? A Sales Growth Calculator is an analytical tool that quantifies the percentage increase in sales revenue over a defined period. Beyond simple tracking, it leverages historical ...
Point of sale Solution Alternatives
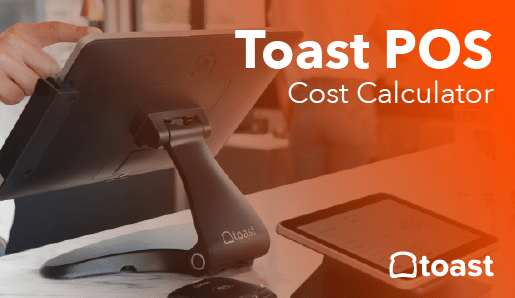
Toast POS Cost Calculator: Know Exactly What You’ll Pay in 2025
Thinking about switching to Toast POS for your restaurant, but unsure about the cost? You’re not alone. Toast is one of the most popular point of sale (POS) systems for ...
Point Of sale Product Comparisons
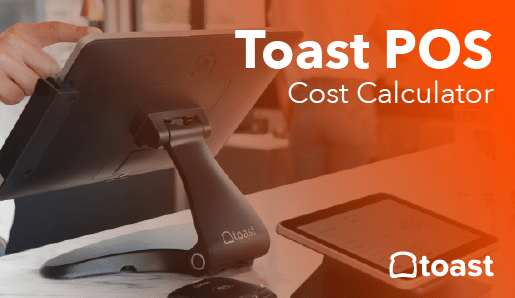
Toast POS Cost Calculator: Know Exactly What You’ll Pay in 2025
Thinking about switching to Toast POS for your restaurant, but unsure about the cost? You’re not alone. Toast is one of the most popular point of sale (POS) systems for ...
Point of sale Product Pricing Guides
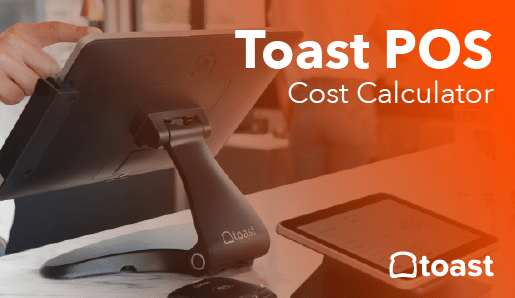
Toast POS Cost Calculator: Know Exactly What You’ll Pay in 2025
Thinking about switching to Toast POS for your restaurant, but unsure about the cost? You’re not alone. Toast is one of the most popular point of sale (POS) systems for ...
Testimonials
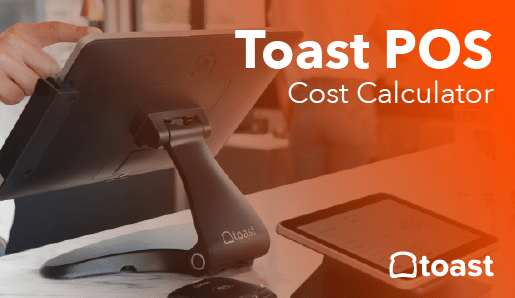
Toast POS Cost Calculator: Know Exactly What You’ll Pay in 2025
Thinking about switching to Toast POS for your restaurant, but unsure about the cost? You’re not alone. Toast is one of the most popular point of sale (POS) systems for ...
Inventory Management
Self-Service Kiosks in QSRs Surge 43% in Two Years — What Operators Need to Know
Self-service kiosks are no longer just a convenience — they’re a growth engine for quick-service restaurants (QSRs). Over the past two years, adoption has surged 43% globally, and QSR operators are ...
Credit Card and Payment Processing

What Cannabis Dispensaries Will Expect from POS Systems in 2026 and Beyond
The cannabis industry isn’t slowing down. As more states go legal and dispensaries pop up on every corner, cannabis retailers are looking for tools that can keep up — and ...
Point of Sale Features and Tools
Self-Service Kiosks in QSRs Surge 43% in Two Years — What Operators Need to Know
Self-service kiosks are no longer just a convenience — they’re a growth engine for quick-service restaurants (QSRs). Over the past two years, adoption has surged 43% globally, and QSR operators are ...
Downloadable eBooks and Guides
The KORONA Studio Back Office Guidebook
Understanding Credit Card Processing eGuide
A Guide On How To Be A Great Retail Manager
Testimonials
"I’ve never worked with a company that has been as focused on customer service. When we call you guys the response has been phenomenal If I could just choose companies based on how they provide customer service, you’d be the top of my list."
– Jennifer from Duplin Winery