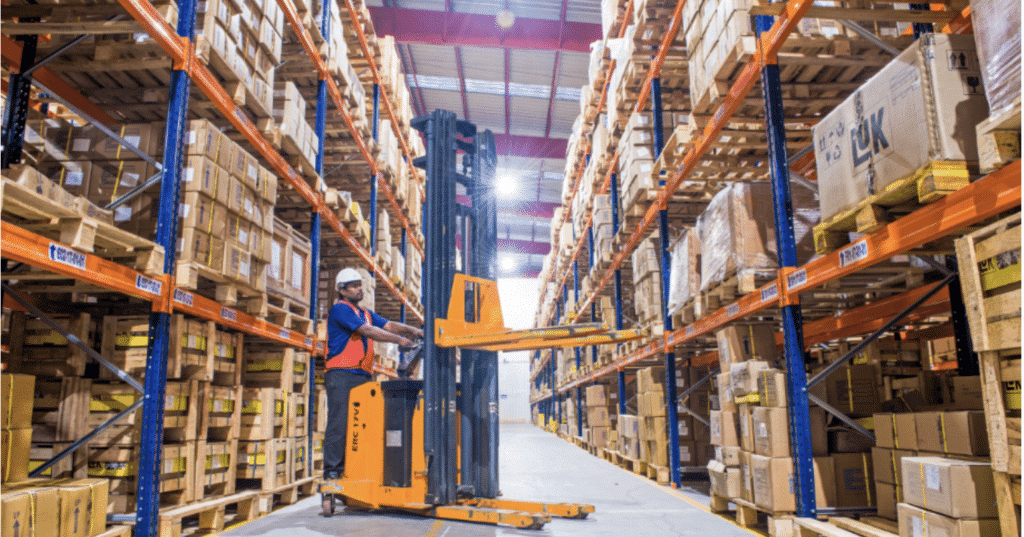
Effective equipment inventory management is a critical responsibility for many businesses and organizations. Keeping accurate records of equipment assets—from acquisition to retirement—optimizes efficiency, performance, and costs. That is true whether you need to track IT assets, machinery, electronics, furniture, or other equipment types.
This blog provides a comprehensive overview of equipment inventory management. It includes numerous benefits, implementation strategies, and how inventory software solutions can streamline processes.
What is Equipment Inventory Management?
Equipment inventory management is the systematic approach of procuring, storing, and administering an organization’s tangible assets and equipment. This encompasses tracking all equipment from acquisition to retirement, maintaining records of maintenance schedules, warranty information, usage data, and more. It’s a method for companies to maximize their equipment’s utility, performance, and lifespan while minimizing operational costs and downtime.
In a retail setting, equipment inventory management is crucial for tracking point of sale systems, shelves, display cases, barcode scanners, cash registers, shopping carts, and other assets utilized in stores and warehouses. For example, a retail chain can maintain a digital inventory of all POS machines across their locations, recording each device’s make, model, age, maintenance notes, value, etc.
The asset tag or serial number identifies the specific machine when issues arise. With regular audits, workers can note missing or broken equipment.
This oversight of equipment inventory enables the efficient operation of retail outlets and quickly resolves problems. Carefully document and organize all equipment inventory to keep business running smoothly.
Overall equipment inventory management surrounds several key factors:
- Tracking: keeping an accurate record of all the equipment in the inventory, including its location, condition, and usage
- Storing: ensuring that the equipment is properly stored in a safe and secure location
- Maintaining: maintaining the equipment in good working condition by performing regular inspections and repairs
- Optimizing: using the equipment in the most efficient way possible
What Is an Equipment Inventory List?
An equipment inventory list is a comprehensive record detailing all the equipment owned or utilized by an organization. It typically includes essential information such as item names, serial numbers, acquisition dates, and equipment conditions.
This list helps businesses keep track of their assets, facilitating efficient management, maintenance, and replacement planning. It is vital for tracking equipment usage, location, and depreciation, aiding in budgeting and decision-making processes.
An accurate inventory list ensures that organizations can optimize equipment utilization, minimize downtime, and effectively plan for future needs.
How to Create an Equipment Inventory List
To create an equipment inventory list, follow these steps:
- Gather all equipment: Collect every piece of equipment owned by your organization.
- Categorize items: Group equipment by type or department.
- Record details: Document each item’s name, serial number, acquisition date, and condition.
- Assign identifiers: Assign unique codes or labels to track items easily.
- Update regularly: Review and update the inventory to reflect changes such as acquisitions, disposals, or damages.
- Store securely: Maintain the list in a secure, accessible location, preferably digitally, for easy reference and management.
Inventory management headache?
KORONA POS makes stock control easy. Automate tasks and get a clear picture of your entire inventory.
Benefits of an Equipment Inventory Management System
There are several significant benefits for businesses that use equipment inventory management:
- Improved Asset Visibility
An inventory management system gives businesses better visibility into their equipment assets. They can track each item’s location, condition, and availability in real-time.
This visibility reduces the risk of loss or misplacement, allowing for better asset allocation and utilization decision-making.
- Optimized Asset Utilization
Businesses can maximize asset utilization by accurately tracking equipment usage and availability. They can identify underutilized assets, schedule maintenance more efficiently, and allocate resources effectively.
This optimization helps to maximize the return on investment (ROI) for each piece of equipment.
- Reduced Downtime
Proactive maintenance is crucial in minimizing equipment downtime. Inventory management systems can automate maintenance scheduling based on usage patterns, manufacturer recommendations, or predetermined intervals.
By staying ahead of maintenance needs, businesses reduce the risk of unexpected breakdowns and costly downtime.
- Compliance and Reporting
Many industries have strict regulatory requirements regarding equipment maintenance, safety, and documentation. An inventory management system can help businesses ensure compliance with these regulations by maintaining accurate records of equipment usage, maintenance history, and safety inspections.
For example, for retailers who sell food or pharmaceuticals, inventory management will simplify tracking the maintenance schedule of refrigeration equipment. Adhering to health and safety regulations is much easier, and it can even reduce retail shrink due to lessened spoilage.
Furthermore, these systems often include reporting functionalities so businesses can generate custom reports for auditing purposes or to demonstrate compliance with industry standards.
- Improved Cash Flow
Equipment that isn’t being used is essentially frozen capital. By tracking what you have, you can sell or lease unused equipment, freeing up cash for other operations. Businesses can also repurpose the equipment to other locations.
- Enhanced Employee Accountability and Training
When employees know that equipment is being carefully tracked, they are more likely to handle it responsibly, reducing wear and tear and misuse. Fostering a culture of diligence and care will minimize downtime and prolong equipment lifespan.
Strategies And Tips for Effective Equipment Inventory Management
Here are five strategies and tips for effective equipment inventory management in retail:
1. Implement Automated Inventory Tracking Systems
Manual tracking is susceptible to human errors and is inefficient, especially when dealing with a large inventory. Automated inventory management systems, like RFID or barcode scanning, make it easy to keep track of equipment, its location, and its status (in use, under maintenance, etc.).
2. Regularly Schedule Inventory Audits
Despite the power of automated systems, occasional manual checks are essential to ensure accuracy. Regular audits—whether full, partial, or cycle counts— identify discrepancies between the system’s data and the inventory.
This is crucial for keeping the automated system in check and maintaining accurate financial records.
3. Train Employees
Your inventory management system is only as effective as the people using it. Employees should be thoroughly trained on best practices. This includes using automated systems and what to do in case of discrepancies or system failures.
Ensuring everyone is on the same page reduces errors and increases efficiency.
4. Analyze and Forecast Demand
Effective inventory management is proactive rather than reactive. Use historical sales data, seasonal trends, and other relevant metrics to forecast future demand for equipment. This ensures you order the correct quantity at the right time.
Advanced tools can even help simulate different scenarios, helping you to prepare for various situations.
5. Leverage Tracking Tags
An excellent automated inventory management system will use asset tagging. Tracking tags like RFID tags are a helpful way to manage your equipment inventory list efficiently. This means every asset will have its own unique ID number or QR code stuck directly onto it.
Having these tags on all your equipment makes it much easier to keep track of everything you own, primarily if your assets are spread out across different locations.
The tags are also better than traditional paper tracking methods for monitoring inventory and the condition of all equipment. So, asset tracking systems with tags on each item are valuable tools for controlling your equipment inventory well. They make it simpler to know what you have and where it is.
An Example of Equipment Inventory Management in Retail
Let’s consider a coffee shop chain with multiple locations implementing equipment inventory management to enhance asset visibility. Here’s how it works:
- Coffee Machine Monitoring: Each coffee shop in the chain relies heavily on its coffee machines to prepare beverages. Equipment inventory management tracks each coffee machine’s usage and maintenance history. Check-ups with a servicing company, filter replacement, and other types of upkeep will ensure all machines are in proper order.
- Equipment Maintenance: Regular maintenance is crucial to keep coffee machines in optimal working condition. An equipment inventory management system schedules preventive maintenance tasks based on usage metrics and manufacturer recommendations. It sends automated reminders to store managers when maintenance is due. This ensures that the machines are serviced promptly to minimize downtime.
- Inventory Audits: Periodic inventory audits are conducted to reconcile physical inventory with recorded stock levels. Store managers use handheld devices or mobile apps connected to the inventory management system to scan barcodes or RFID tags on equipment and supplies. Any discrepancies are flagged for further investigation, helping to identify and address issues such as theft or misplacement.
- Asset Tracking: In addition to coffee machines, the inventory management system tracks other equipment and assets used in the coffee shop, such as espresso grinders, blenders, refrigerators, and coffee shop POS terminals. Each item is assigned a unique identifier and added to the system’s database. This ensures that all assets are accounted for and properly maintained, reducing the risk of loss or damage.
- Performance Analytics: The inventory management system generates reports and analytics dashboards that provide insights into equipment performance, inventory turnover rates, and cost of goods sold (COGS). Store managers can analyze this data to identify trends, optimize resource allocation, and make informed decisions to improve operational efficiency and profitability.
The coffee shop chain can achieve greater asset visibility and control by implementing equipment inventory management. Moving different types of machinery, replacing equipment, and buying new assets will all be guided by data insights and careful planning.
Equipment Inventory Management FAQs
- Why is equipment inventory management important?
Effective equipment inventory management ensures businesses have the right tools and resources available when needed, minimizing downtime and improving operational efficiency. Proper management helps track equipment usage, maintenance schedules, and lifecycle so businesses can optimize resource allocation and reduce unnecessary costs. Maintaining accurate records helps with compliance and enhances overall safety and accountability.
- What is included in equipment inventory?
Equipment inventory typically includes a detailed list of all physical assets used in operations, such as machinery, tools, vehicles, and technology devices. Each item is tracked with a unique identifier, description, and relevant details like purchase date, location, and condition. The inventory may also include spare parts, accessories, and consumables for maintaining and operating the equipment.
- How do you maintain equipment inventory?
Maintaining equipment inventory involves regularly updating records with accurate information on each item’s status, location, and usage. Implement a system for tracking equipment movements, repairs, and maintenance schedules. Conduct periodic audits to reconcile physical counts with inventory records to better ensure accuracy and promptly identify discrepancies.
Using The Right Inventory Management Software For Your Retail Store
The importance of equipment inventory management in a retail business often goes hand-in-hand with managing consumable goods through inventory management software. While the latter focuses on ensuring you have the right amount of products available for sale, the former concentrates on keeping essential business tools and machinery in optimal condition.
Poorly managed equipment causes operational disruptions, increased maintenance costs, and even downtime that prevents sales. Similarly, mismanaged retail inventory leads to missed sales opportunities, higher carrying costs, and reduced customer satisfaction.
That’s where KORONA POS’s inventory management software comes in. It efficiently handles the management of retail goods—tracking stock levels in real-time, automating reordering processes, and providing insightful sales analytics—and its robust capabilities can also be extended to managing a company’s equipment inventory.
Whether running a coffee shop, a bookstore, or a convenience store, KORONA POS will help you track your retail products. Automated alerts can notify you when it’s time for routine maintenance on these essential equipment pieces, integrating seamlessly with its already robust retail inventory management functions. Click below to learn more about how KORONA POS can help you streamline your business operations.